Hello, friend.
My name is Peter Buterbaugh. This is my little corner of the Internet.
$whoami
I am a graduate of Worcester Polytechnic Institute's Robotics Engineering program, Class of 2024. My time in the FIRST Robotics Competition during high school introduced me to robotics, and I have been addicted ever since. I never want to stop learning and improving.
$cat summary.txt
Following a role at Berkshire Grey, contracted by Actalent as a Contractor Deployment Systems Engineer, I wish to pursue roles involving mechanical design, software design, and/or electrical work for electromechanical assemblies (robot and robot-adjacent!).
$cat experience.md
Contractor Deployment Systems Engineer
Start/End: January 2024 - January 2025
Contracted by Actalent to work with Berkshire Grey. Assisted with the commissioning of new warehouse robotic sorting systems and maintenance of existing production systems.
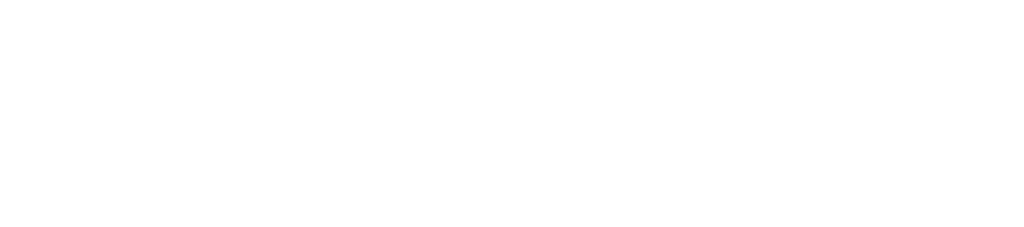
Electrical Engineer Intern
Start/End: June - August 2023
Primarily worked on the addition of network stress-testing features and Java Swing GUI elements to an internal Java-based application, used for testing out newly constructed competition fields.
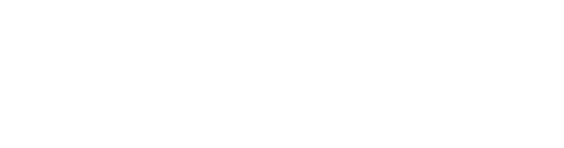
Mechanical Engineer Intern
Start/End: June - August 2022
Spearheaded project to introduce industrial and collaborative robots into a manufacturing workspace equipped with modern CNC tooling. Led effort to bring company to an automation trade show, sparking new interest into Industry 4.0 technologies.
$cat projects.md
# What have I done?
## Mechanical Stuff
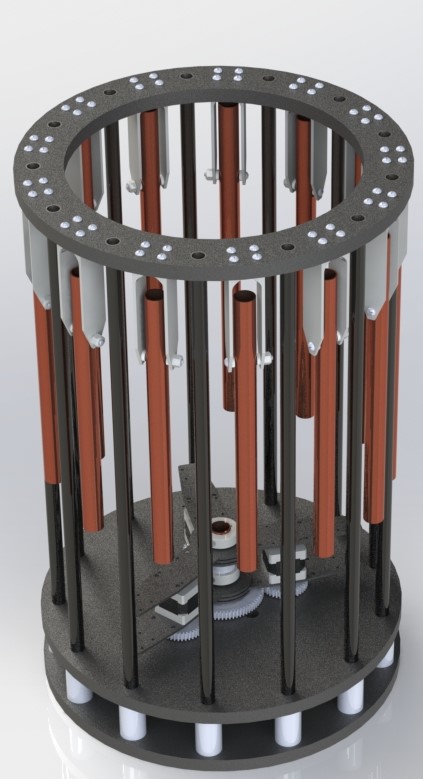
Robotic Autochimes Concept for Humanities Capstone
Skills: SOLIDWORKS, laser cutting, Design for Manufacturing
In a group of three, a proposal was made to create a robotic, MIDI-powered instrument based on the concept of striking wind chimes to produce sound.
I was responsible for the mechanical design of my group's concept and submission, which was completed in SOLIDWORKS 3D CAD.
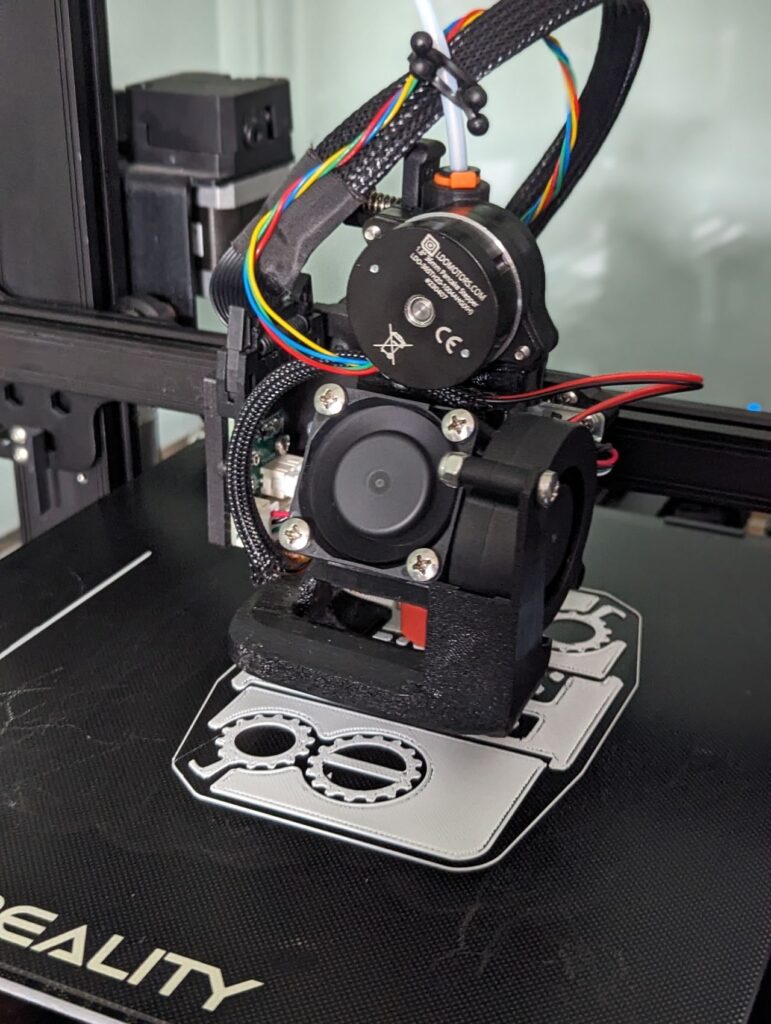
Reverse Engineering and Improvement of FDM 3D Printer Toolhead
Skills: SOLIDWORKS 3D CAD, Perforce Version Control, Rapid Prototyping, Design for Manufacturing, Additive Manufacturing/3D Printing
A popular set of modifications known as the “HeroMe mod” did not support Creality CR-6 SE printers due to the comparatively unique implementation of a strain gauge as a means to achieve Auto-Bed Leveling (ABL) functionality. For the purposes of refining my SOLIDWORKS CAD skills, it became my goal to implement this modification with full support for strain-gauge ABL with the intention to open source it for other users to enjoy.
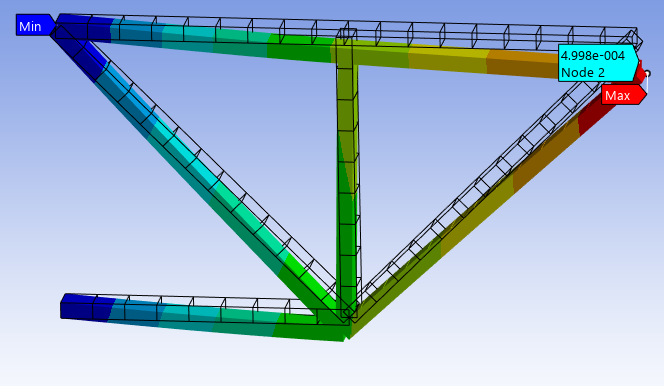
Basic FEA of Materials in Various Scenarios
Skills: ANSYS Mechanical, Free-Body Diagrams
While enrolled in Introduction to the Finite Element Method, I analyzed and simulated several scenarios involving materials such as structural steel (with given Poisson’s Ratio, Young’s Modulus.) These included frame structure, truss, plane, and beam analyses. The underlying theory in calculating results by hand, too, was also reviewed to ensure proper understanding of how ANSYS simulates loads.
## Software Stuff
Bioinspired Exosuit Communications Stack (Senior Capstone)
Skills: C++ (Arduino), UART, I2C, Interacting with Sensors
Abstract: The Bioinspired Exosuit utilizes pneumatically-actuated artificial muscle (“Hydro Muscles”) to provide assistive forces while walking. This project continues on a multi-year effort to utilize Hydro Muscles for this purpose. The exosuit uses neural network-based control, informed by a comprehensive suite of sensors that determines the state of the suit and pose of the user. Neural network-based control allows for the adaption to the user’s specific gait cycle and provides optimized support to decrease the energy consumed while walking.
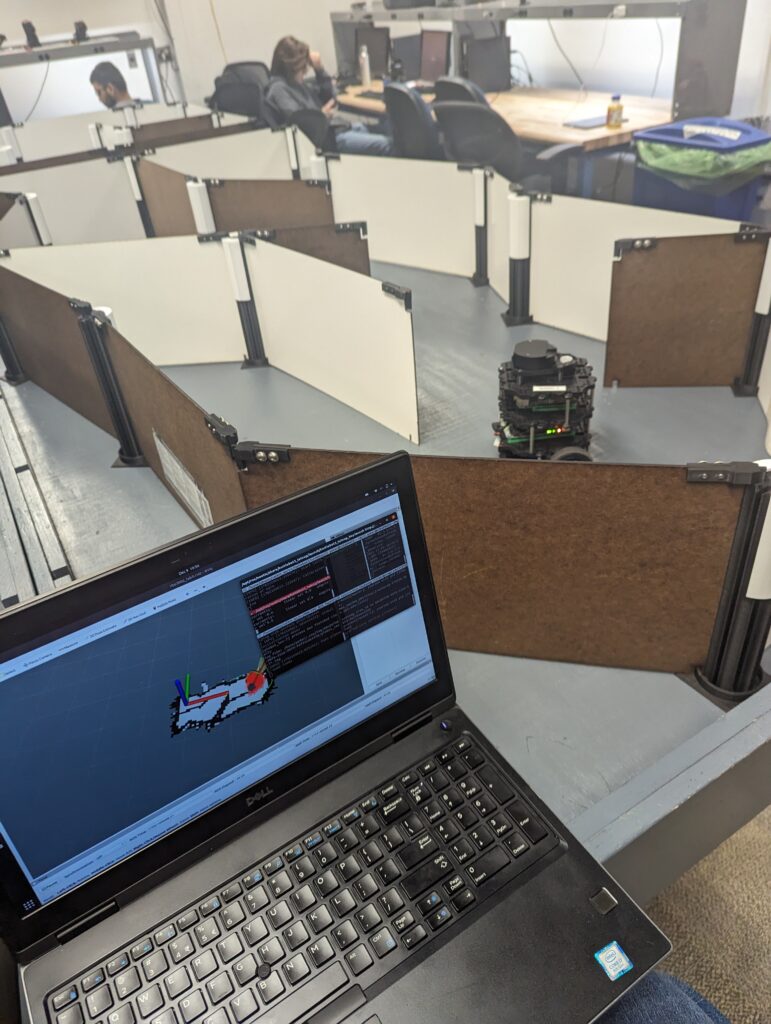
SLAM & Autonomous Navigation of a TurtleBot3 using ROS
Skills: Python, ROS 1 (gMapping, AMCL), A* Algorithms
The final project in Unified Robotics IV tasked students to enable a TurtleBot3 Burger research platform to navigate a variety of different mazes autonomously, map it, and perform path-finding using an A* algorithm implementation after localizing using AMCL.
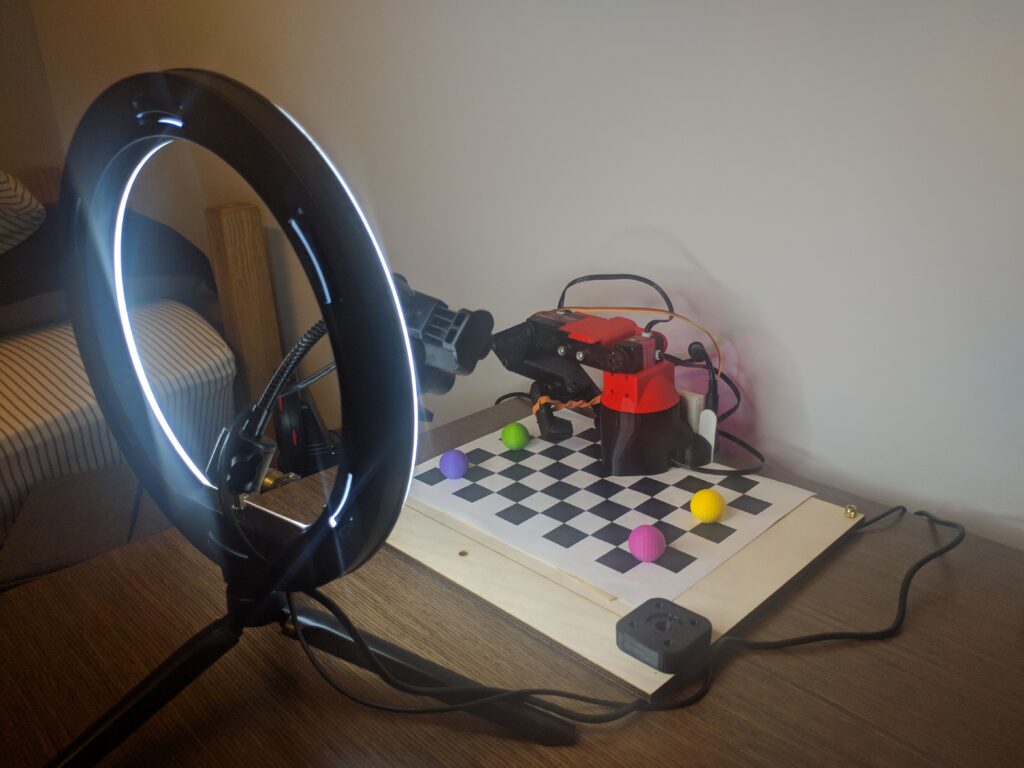
Pick & Place of Objects by a 3DOF Robot Arm using MATLAB CV Toolbox
Skills: MATLAB, Robot Kinematics, Coordinate Transformations
A relatively simple three-DOF robot arm with a gripper composed of servos and an Arduino Nano communicates over USB to a laptop running MATLAB, which, using a webcam, determines the locations of various objects in the reach of the arm to perform pick-and-place operations.
Creating Sound using a MicroBlaze Soft Microprocessor via an Artix 7 FPGA
Skills: AMD/Xilinx Vitis & Vivado, Verilog, Embedded C, Benchtop Tools
Using a Digilent Basys 3 connected with a PMOD Amp (3.5mm out), an Artix 7 FPGA is able to incorporate intellectual property and a generated MicroBlaze soft microprocessor core to run Embedded C code. With specific inputs given, instructions are sent to the PMOD Amp and audible frequencies are played over the connected speaker.
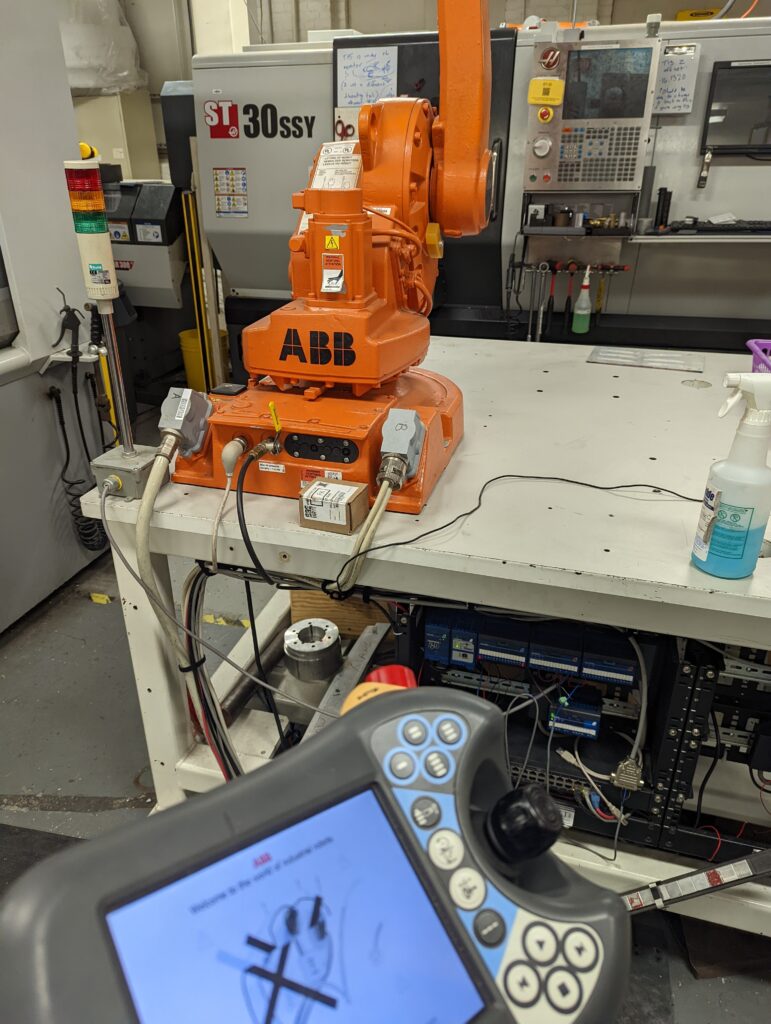
Pick & Place of Blocks using an ABB IRB1200 Robot Arm and an AutomationDirect PLC
Skills: Coordinate transforms, ladder logic, ABB RAPID & RobotStudio
An AutomationDirect DoMore PLC, using ladder logic, communicates with an ABB IRC5 Robot Controller to command an IRB1200 5-kg payload 6-DOF arm and coordinate the palletizing of metal cubes when specific conditions are met. Worked in a team of 3.